When a Minnesota-based mine experienced detrimental damage to the radiator on one of its excavators due to an exploding engine fan, the L&M Radiator team sprang into action to get the machine back up and running in less than 24 hours – saving the site an incredible amount of machine downtime and money in the process.
Eveleth, Minnesota – There’s nothing pretty about an iron more mine. It’s a dusty, dirty, rugged, unrelenting place where the tough get tougher. And that goes for the machinery in this place. It’s put up or shut up. Operating 24/7/365, the machinery just has to keep going to feed the world’s need for iron ore.
When this much is demanded from equipment in this rugged environment, the occasional incident is bound to happen…but that doesn’t mean that the work can stop. People are counting on mines to meet deadlines and optimize every hour spent in operation. So, the question remains: When stuff happens, who do you trust to get you up and running again?
For the folks at United Taconite Mine (UTAC), the answer is clear — L&M Radiator.
The United Taconite Mine is an open-pit iron ore mine located in Eveleth, Minnesota. Operated by Cleveland-Cliffs, the largest flat-rolled steel company in North America, and U.S. Steel, this mine has been active for more than 51 years. At the site, UTAC mines for taconite, performs the initial stage of crushing, and sends the crushed ore (now taking the form of magnetite) 10 miles away to Forbes, Minnesota, where it is processed into pellets, which are then shipped through the Great Lakes to steel mills.
In September 2022, an incident occurred in one of UTAC’s most critical excavators. One of the fan blades spontaneously broke off from the machine’s engine, causing it to crash into one of the machine’s two Mesabi radiators. The intense impact (likely striking the radiator at close to 1,800 RPM) knocked out the entire first row of the radiator’s tubes, which began to leak. The excavator in question was a Komatsu PC 5500 Excavator, equipped with a factory-installed Mesabi® M-Tube style copper radiator.
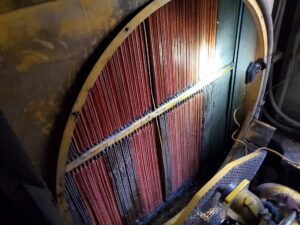
“When we got the initial call from the maintenance manager on site, he was in a panic because when that machine is not running, they’re not making money,” said Chad Mastakoski, Customer Service Representative at L&M Radiator. “It’s a big deal for those guys when an excavator goes down like that.”
With any other radiator, damage of this extent would require the whole unit to be pulled out and entirely replaced. This would necessitate using a crane and other large equipment to pull off the counterweights and the outside sheet metal to remove the cooler. Not to mention, with today’s lead times, it would likely have taken the mine several months to receive a new radiator and would have likely cost the mine tens of thousands of dollars.
But not with a Mesabi® radiator.
Genuine Mesabi radiators are built with grommeted, replaceable radiator tubes, meaning individual tubes can be easily removed and replaced in the field in as little as one hour. Usually, this process is simple enough that it can be done by mine personnel without the aid of L&M Radiator support, but, on this particular day, other equipment maintenance demanded the attention of mine maintenance personnel, meaning they required all hands on deck to get this excavator up and running again.
“We usually recommend that sites have at least a handful of tubes just in case something like this does happen, but this happened to be a ‘worst of all of the bad situations’ scenario,” said Josh Mitchell, Design and Application Engineer at L&M Radiator, the manufacturer of Mesabi radiators. “The mine had other shovels that were down that day, and they didn’t have extra tubes on hand. Everything went wrong for them at the same time.”
L&M Radiator to the Rescue
As soon as L&M got the call from UTAC, the whole facility in Hibbing, Minnesota (less than a 30-minute drive from the mine site) sprang into action. Knowing the extent of the damage and the consequences that it would have on the mine, L&M Radiator staff worked as hard as they could to ready the tubes in time for the machine to get back up and running as fast as possible.
“Usually when we get a call such as this, our turnaround time is approximately two or three days,” said Josh Mitchell, a Design and Applications Engineer at L&M Radiator, “But UTAC only had one shovel operating at this point, so we wanted to help them out as soon as we possibly could. As soon as we knew what tubes they needed and how many, we switched one of our production lines over to make these tubes for UTAC.”
The facility switched gears immediately, churning out tube after tube to complete the order as fast as possible. By eight o’clock in the morning the next day, L&M Radiator’s Mastakoski, Mitchell and Field Representative Ryan Daley arrived on the scene of the accident, brand new tubes in hand.
“From there, all that we had to do was pull the damaged tubes and replace them with the new tubes,” said Mitchell. “Mesabi radiators are designed so this process is swift and easy. We even put new seals in as well just to be on the safe side.”
There was only one problem – Once the team started replacing the tubes, they realized that many more tubes than the 40 that the maintenance manager had reported were also damaged. In total, 80 grommeted copper tubes required replacement.
“Originally, our understanding was that they needed 40 new tubes. Well, the folks on site didn’t realize that the tubes in the center of the radiator had been damaged as well. When I got there, I saw that way more than 40 tubes were damaged,” recalled Mastakoski.
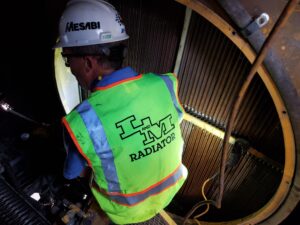
“So, Josh [Mitchell] and Ryan [Daley] came back to the L&M Radiator facility in Hibbing, got the tubes, and came back out to Eveleth,” added Mastakoski. “By that time, I was already taking the tubes and seals out and just waiting for them to come back with the other tubes. Then we put the tubes in, put the new seals in, and they were good to go. Just like that.”
The whole incident, from the first ring of the phone to when the machine was back to work again, took less than 24 hours in its entirety.
“The manager was so happy to get his machine up and going again,” said Mastakoski. “He really had his hands full that day and definitely appreciated that we did everything we could to get them back up and running again. At L&M Radiator, we do the best we can for our customers. It’s what we do. It’s the Mesabi Difference.”
All this goes to show, if there’s a problem that affects a Mesabi radiator, our team is ready to spring into action to keep our customers moving. If you find yourself in a machine-down situation, you can count on us to respond and get your wheels churning again in as little time as possible.
Know the Mesabi® Difference
When push comes to shove, our team has your back. For stories similar to this one, visit The Mesabi Exchange at www.Mesabi.com.